LICO technology is based on
the separate feeding of each component. The material output is
regulated through a system which continuously controls the weight decrease in the
hopper. The speed
of the conveyance device is regulated so as to get a constant product
flow in terms of weight - ignoring possible variations of bulk
density or particle size.
The control system guarantees a high metering
precision in a short time.
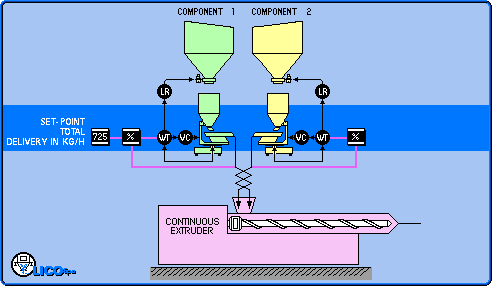
Advantages of the process:
- optimal monitoring of quality,
- no need for pre-mixing operations,
- in-line feeding of products with
different particle sizes (production scraps, selvage, etc.)
|
In-line mixing
As a consequence to the random fall into the extruder's hopper the dosed
components are mixed in-line and are immediately processed
without accumulating within the hopper.
In this way any intermediate piling up of material that may cause
possible separations of the mixed products is avoided, meaning there are no variations
in the composition of the end product.
|
|
Advantages of the process:
- optimal process control (absolute certainty of the recipe composition),
- lowest pollution and easy production change,
- simplification of the raw products displacement upstream,
- maximum flexibility of the product set up that
can be varied in line.
Feeding the extruder hopper at empty hopper
Monoscrew extruders are traditionally fed at full
hopper. The hourly output depends
exclusively on the rotation speed of its screw.
This method has two main drawbacks:
- the hourly throughput is constantly related to the rotation speed
of the screw,
- another control system is needed to keep a constant
pressure in the extruder head.
Though still mainly unknown, the feeding technology at empty hopper
offers remarkable advantages, including:
- no piling up of material, with subsequent separation of the ingredients, a condition that would
make the in-line feeding of differently sized scraps problematic (in-line recovery of
selvage),
- a more flexible relation between turns of screw and
hourly output, thus making it easier to set the optimal
working conditions of the line for different products,
- a perfectly constant feeding of the extruder without inner pulsations,
keeping constant pressure within the head and turning this way
the extruder into a pump carrying out the material received,
- working constantly at maximum rpm increases the capacity of the line.
It will not be necessary to keep security margins to carry out
the typical screw rotation regulation; on the contrary, it will be
possible to work constantly at maximum potential,
- the stable conditions of the line guarantee the
steadiness of all working parameters (temperature and compression).
|
Example of application: in-line coloring
|
Continuous turbo mixer
The continuous turbo mixer represents the natural development of
LICO engineering, whose goals:
- better process control (quality, waste reduction, greater exploitation of plants)
- lower power consumption (economy)
- plant simplification (maintainance free, flexible setting, smaller room requirements)
Compared to other discontinuous mixers available on the market, it
disperses even the minimal percentage of the ingredients - either liquids or
solids - being processed, assuring the most homogeneous mix with minimal energy
consumption. Along with the
high-tech LICO feeders systems TM turbo mixer represents the most efficient
way to prepare blends of powders and/or
liquids.
LICO technology finds its application to ready-mixed
products or blends that have to undergo further process
stages (extrusion, reaction, fusion).
Main technical specifications
Shaft's revolution ratio adjustable from 1 to 20. Variable configuration
rotary shaft according to process needs, equipped with mixing and conveyance pegs, mixing, back mixing zones.
The body can be easily taken apart for cleaning and inspection. A.C.
motor driven by inverter. All metal parts in contact with material
are in stainless steel AISI 304 (AISI 316 upon request). Possible thermoregulation of the
process area.
|
VARIABLE SPEED TURBO MIXER WITH CHANGEABLE SHAFT CONFIGURATION
|