Following here are the 4 types of feeders representing the core
of LICO's production:
|
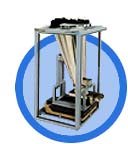 |

 |
 |
TYPE «DV», WITH VIBRATOR
For feeding granules, chips, flakes, free-flowing powders,
fibres, regrounds and other materials.
|
TECHNICAL DATA |
 | General features |
 | Models available |
|
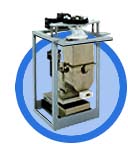 |

 |
 |
TYPE «DS», WITH TWO SPIRALS OR SCREWS
For feeding all kinds of powder.
|
TECHNICAL DATA |
 | General features |
 | Models available |
|
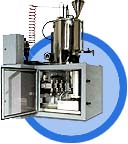 |

 |
 |
TYPE «DP», WITH PUMP
For feeding liquids and pastes of different viscosity.
|
TECHNICAL DATA |
 | General features |
|
|
|
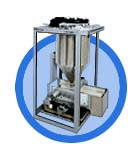 |

 |
 |
TYPE «DN», WITH BELT CONVEYOR
For feeding blends and particular materials.
|
TECHNICAL DATA |
 | General features |
 | Models available |
|
The gravimetric feeding guarantees a precise and constant recipe fed to the process.
The advantage to the end product results in a
constant quality and composition throughout the process.
By working only with the weight value of the ingredients the
system eliminates typical troubles as those deriving from different
bulk density and/or different physical shape/state
(pellets, flakes, chips, powders, liquids,pastes).
Depending on the features of the material at hand (free flowing, difficult,
cohesive, liquid or viscous components which physical features change with temperature),
a different type of feeder is implemented.
Though the feeders may be different in structure and discharging components, size
and capacity, the operating principle remains the same.
Operating principle
By means of a load cell, the system logic
constantly checks the rate of the ingredients fed
to the process by comparing instant by instant the shifts in weight of the
material inside each feeder with the previously set theoretical value at recipe
(set point). When the two values do not match the system logic instantly
adjusts the rate by increasing or lowering the feeder's speed.
Refilling
In order to work in continuos each feeder must be refilled at regular intervals.
The refill is done through a "Refilling Valve" which allows material discharge into the feeder.
When the weight is close to a set low-level, the load cell controller calls for a refill: the
valve opens and then it locks back into position.
The whole operation takes about 10secs - 2/3secs the time the valve remains open and 7/8secs
to allow material settling into the feeder - during which time the
feeding unit works at constant speed (volumetric), the same speed value memorized
by the system just a few secs before the refilling operation was given the start. Once the refilling
is completed, the system returns to work gravimetrically by adjusting the feeder's discharge speed in
accordance with the value at recipe (set point).
Working range
Standard version : 1 to 10
Special execution: 1 to 20
Delivery range
from 50 gr/h to 100 tons/h
Working precision
± 0.5% over the full working range in reference to the set value.
Weighing plate equipped with strain gauge load cell [IP67].
CONSTRUCTIVE FEATURES
All parts in contact with materials are realized in stainless steel AISI 304 (AISI 316 upon request).
Easy to service and clean. The
weight control system is not affected by temperature or bulk density
variations and needs no adjusting, calibration is automatic.
An autocontrol circuit ensures the feeder's correct functioning.
Electronic circuits are set on 19" racks to facilitate eventual servicing.
The electronic control panel can be connected directly to the single
phase mains and operate where high voltage variations occur. The
equipment is not affected by dust, works correctly with temperatures
from - 25° to + 85° and can be installed as far as 3 km from the
feeders.
The control panel comes with a synoptic board on which is displayed plant function, making handling easy to unskilled personnel.
All constructive components are standard and consequently easily available.
Our unique modular system offers wide flexibility for future modifications.
CUSTOM MADE OPTIONS
Dust-proof housings to prevent environment pollution.
Proofed housings for pressurization (feeders operating under inert conditions).
Explosion-proof protection.
Heating device for highly viscous substances.
IP 65 outer environment protection.
Upgrades for processing temperatures from -55° to +125 °C.
OPTIONALS
Interface with process computer, for automatic managing of recipes and/or to obtain process data.
Autodiagnostic alarm display.
|